SGDF Sigma Mini
Breadcrumb
Navigation Menu
Products
SGDF Sigma Mini
SGDF Sigma Mini
SGDF Sigma Mini -YAI
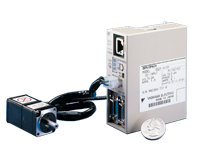
10 or 20 watts, input 24 VDC
The SGDF Sigma Mini amplifier is a legacy product and no longer promoted in the Americas. The SGDF was an ultra-comptact all-digital amplifier designed for use with Sigma mini motors. Options included an analog input version for torque speed control or a pulse input version for position control.
TemplateWeb
Manuals
Login
to view all content that is available based on your partner settings.
No Result Found
Showing 4 of 4 results.
Title/Number | File(s) | Rev Date | |
---|---|---|---|
Holding Brake Wiring Warning eng08148![]() Rev Date:11/20/2008
|
![]() |
11/20/2008 | |
Sigma Servo Software (SVMON) for PC Monitoring SIE-S800-15.5![]() Rev Date:12/01/1995
|
![]() |
12/01/1995 | |
Sigma Mini User's Manual SIE-S800-27![]() Rev Date:05/14/2007
|
![]() |
05/14/2007 | |
AC Servo Drive Conforming to EN Standard Sigma Mini Series INSTRUCTIONS TOB-S800-27![]() Rev Date:04/24/2015
|
![]() |
04/24/2015 | |
Node: dxpprd01:8080