U1000 Industrial MATRIX Drive
Breadcrumb
Navigation Menu
Products
U1000 Industrial MATRIX Drive
U1000 Industrial MATRIX Drive
U1000 Industrial MATRIX Drive - YAIALL
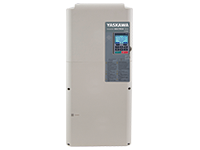
5 to 800 HP
The U1000 is a compact, total all-in-one solution for low harmonics and/or full regeneration, and is the ultimate choice for power quality and energy savings. Additionally, the U1000 delivers high flexibility and motor control performance to meet various application requirements.
Award Winning Technology | An Overview of Matrix Drive Technology
TemplateWeb
Features
U1000 Industrial Matrix Drive - Overview
Highlights:
- Full Regeneration
- Low Input Distortion Across a Wide Load and Speed Range
- Facilitate IEEE 519 Compliance
- Eco-Mode to Achieve Near Across-the-Line THD
- High Efficiency Design Provides Extra Energy Savings as Compared to Other Low Harmonic Solutions
- Near Unity True Power Factor at Full Load
- Integrated Input Fusing Provides 100kA SCCR
- Compact Design
- High Reliability with an MTBF of 28 Years
- Embedded Modbus RTU Communications
- Removable Terminal Block
- High Carrier Frequency (Low Motor Noise) Capability
- 0-400 Hz Output Frequency
- 120% Overload for 60 Seconds (ND)
- 150% Overload for 60 Seconds (HD)
- Multi-language LCD Display with Copy function
- Start into Spinning Load (Speed Search)
- Both Induction and Permanent Magnet Motor Control
- Closed or open loop vector control for outstanding regulation, torque production, and position control capability
- Continuous Auto-tuning optimizes performance by compensating for changes in motor temperature
- High Frequency Injection enables high precision open loop control of Interior Permanent Magnet Motors
- Fast acting current and voltage limiters help achieve continuous drive operation during periods of excessive demand
- Communication options for all major industrial networks provides high speed control and monitoring, reducing installation cost
- DriveWizard computer software and Application Sets for easy configuration
- Embedded Safe Torque Off minimizes downtime for applications requiring occasional intervention (SIL CL3, PLe, Category 3)
- Embedded function blocks, programmable with DriveWorks EZ, provide additional application flexibility and the opportunity to eliminate separate controllers
- USB Copy Unit and Keypad configuration storage provide speed and convenience for duplicate configuration of multiple drives
- Made with RoHS compliant materials
Node: dxpprd02:8080
It looks like you are using Internet Explorer 11 or below, this website isn`t compatible with this and for the best experience please use the latest version of Mozilla Firefox, Google Chrome or Safari.