SGDG
Breadcrumb
Navigation Menu
SGDG
SGDG
SGDG Legend - YAI
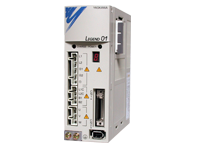
200V 3P/1P 1.0kW
The SGDG Legend servo amplifier is a legacy product and no longer promoted in the Americas. The SGDG Legend was a single-phase or three-phase AC and DC input amplifier with 100% digital design, an intelligent serial coder and ethernet motion control functionality. Four amplifier sizes (100w - 1,500w) and 23 motor choices cover a wide range of needs.
TemplateWeb
Available Services
SGDG - Support
Repair
Our goal is to minimize production downtime by providing you with prompt and reliable on-site services.
Full details about repair program available in support area.
Field Service
Along with Yaskawa Field Service Engineers, we are also able to provide local service through our wide network of Authorized Service Providers.
Full details about field services program available in support area.
Technical Phone Support
Yaskawa provides support for all of its products on a global basis.
Full contact information available in support area.
It looks like you are using Internet Explorer 11 or below, this website isn`t compatible with this and for the best experience please use the latest version of Mozilla Firefox, Google Chrome or Safari.