V1000 Drive
Breadcrumb
Navigation Menu
Products
V1000 Drive
V1000 Drive
V1000 Drive - YAIALL
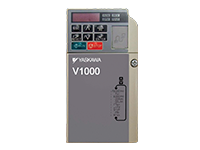
1/8 - 25 HP
The V1000 is a world-class compact current vector drive that defines a new world standard. Demands for efficient production and better maintainability are on the rise, spurred by global competition. Yaskawa pays off the promise of being in control with products that make businesses move. The optimum balance of energy input, product output, maintenance risk, and long life is reached with Yaskawa. The V1000 provides a world of power in the palm of your hand!
The V1000 is the flagship drive of the V1000 Family, which also includes the V1000-4X.
TemplateWeb
Power
V1000 Drive - Options
This array of Power-related options are available for Yaskawa AC drives as shown. Some may be factory-mounted within a drive enclosure, others may be separately mounted.
Power Options |
More Information
|
---|---|
24VDC Control Power Unit...This option provides board-level component voltages for the V1000 drive when provided with 24VDC from an external, customer-supplied source. It is used to maintain both drive control power and network communications (when utilized). Both a Control Power Unit and a Bracket Kit are required for proper operation and certification. | |
Reactor...Used on either the input or output of a drive to reduce the effect of load or line side transients on the drive. The three-phase reactors are available loose in a separate NEMA 1 enclosure. | |
EMC C1 Filters...Used on the input of the drive to attenuate possible drive-generated noise. Filters should always be mounted as close to the drive a possible; these are designed such that the drive can be mounted to it, pancake-style. The drive should be installed with the EMC filters listed in order to comply with the EN 610800-3, category C1 requirements. These C1 filters meet the requirements for CE. Note: EMC filters for models CIMR-VU2A0030 trough 0069 are in compliance with EN 61800-3, Category 2. All other models comply with Category 1. | |
EMC C3 Filters (Conducted Interference Voltage Limits)...Used on the input of a drive to attenuate possible drive-generated noise. Filters are designed to mount directly to the drive below the input terminal connectors. An input filter with proper shielding, routing, and grounding between itself and the drive is designed to reduce line-conducted noise levels within the limits of EN 61800-3 Category C3, I <= 100A (second environment for industrial low voltage supply network), when the drive's output conductors are properly routed and shielded in grounded steel conduit all the way to the motor.
|
|
Dynamic Braking 10% Duty...Assists the drive to periodically decelerate a load without overvoltage trips. Dynamic braking consists of at least one transistor and at least one resistor, and is sized for rated motor horsepower. The braking transistor may be included in the standard drive. The resistors are sized for a 10% duty cycle (10 seconds maximum on-time of every 100 seconds), and will provide approximately 150% braking torque. Ten percent dynamic braking is not typically used for "hold-back" type applications such as unwinders, hoists, or downhill conveyors. | |
Dynamic Braking 3% Duty...Are rated for 3% duty cycle over a 100-second interval. Approximate braking torque for each rating is listed. These resistors are designed in NEMA 1 enclosures for separate panel mounting. | |
Line Regeneration Converters...Yaskawa offers two line-regeneration products, that can provide braking torque in applications that have large overhauling loads or make frequent stops such as elevators, centrifuges, test stands, and winders. Line regeneration can result in significantly reduced operation costs in these types of machinery by “re-cycling” the excess power back to the power grid. The D1000 is a high performance converter with a PWM sinusoidal waveform with very low harmonic distortion (approximately 5% THD) and is designed to meet IEEE-519 requirements. The DC5 is wired in series between the drive and the incoming line and therefore must have an equal or larger current rating than the drive. The D1000 handles both motoring and regenerative power from the drive. The R1000 unit is lower cost with a 6-step output waveform that does not provide IEEE-519 compliant power and can be sized based on the application, from continuous to intermittent. The R1000 is wired in parallel to the drive and only handles regeneration power. The drive handles motoring power through its own diode bridge. |
Node: dxpprd01:8080